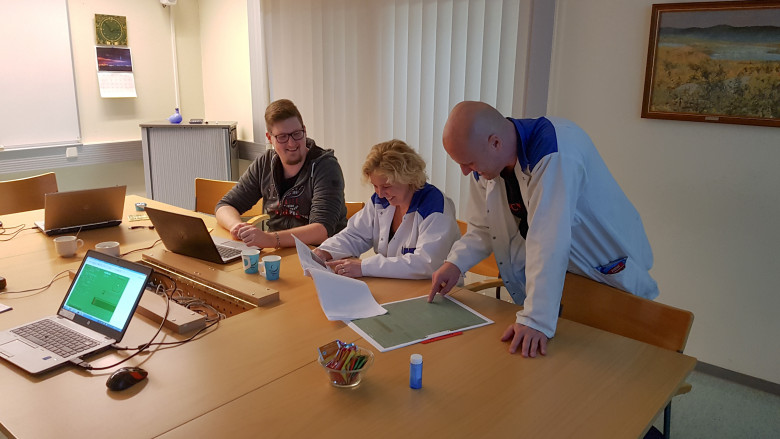
In May 2020, we are slowly recovering from the first wave of covid-19 in Europe and lockdown restrictions will be removed step by step. The 1st battle looks like won or at least ceasefire, but overall the covid case is far from over. Everyone is waiting for the vaccine.
Meanwhile in Aspocomp, we cannot wait with our regular business. We need to take care of our customer’s PCB projects also in these exceptional times. At the same time, naturally we are also taking care of our own future as a PCB company. Even if Aspocomp has taken some limited hits by covid-19 restrictions, we are up and running with full capacity. So far we did not face any production stops due to the covid-19 situation in our home factory.
What does it mean then to take care of the PCB projects? For sure this is very much depending on the scope of the project and customer guidelines. Please let me describe how a typical high technology and high volume PCB project typically goes. To make it first time, first revision.
Specifying materials, stack-ups and design rules
Usually this type of projects involves special materials, dedicated stack-up and some PCB based functionality like impedance control transmission lines, cooling features or antennas for example. Another dominating factor may be high density components which may require complex HDI structure to get fully connected.
Quite often project starts with some engineering inquiries concerning available materials and our manufacturing capabilities. Experienced HW designer usually has some vision how the PCB would look like and he/she is able to draft some combination of layer allocations and impedance requirements to start with. From that on we can suggest some detailed stack-up to meet the requirements. Usually some fine-tuning will be necessary and sometimes several iterations of stack-up and impedances will be necessary. In tricky cases we may provide a dedicated design rule set for the PCB.
Gerber files
Then the project usually calms down for a while from Aspocomp point of view. We may book already the laminate materials if agreed so with the customer, but not much happens in weeks or even months. PCB layout guy may approach with some design rule questions if any. However in the customer side there is a full effort ongoing to provide gerber files or ODB++ database for PCB manufacturing.
In case of challenging project we recommend to have some file review to ensure PCB manufacturability. It can be done with 95% ready files, for example. Then the designer is able to fix the possible ‘bugs’ within the project timeline. This will make the launch of the first revision smoother.
Manufacturing the 1st lot
Then we are ready to start. My experience is that better we prepare in advance, the less issues there are to be clarified. Lots of open questions normally takes some time to settle. A fluent launch means better chance to make positive results for everyone.
Engineering resources
All these actions involve engineering resources of our technical customer service team. It is necessary to find a reasonable balance between the pre-engineering effort and the revenue of the project. Our home factory in Oulu, Finland typically runs about 100 new products per month and therefore our engineering team needs to focus on the largest projects. It means that the first small prototype lot of significant project will get the full attention. Naturally the smaller projects will be supported as well, but within the scope of the project.
By Markku Jämsä