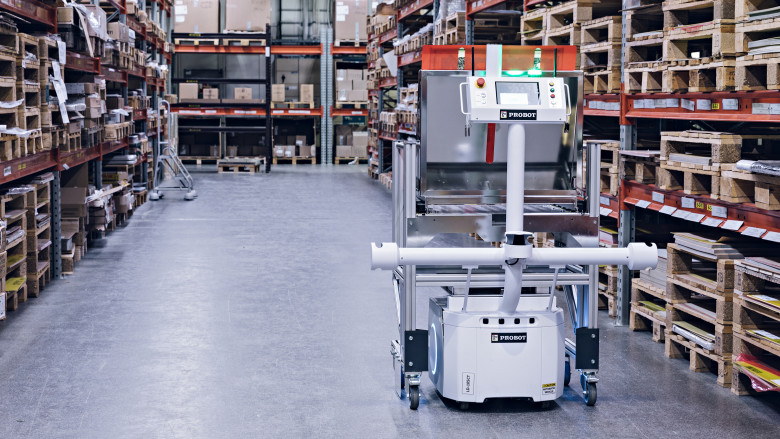
As any PCB supplier, Aspocomp can’t make a single PCB without proper dielectric materials. Moreover, boards are no-longer using just “good-old FR4”, but the variety of materials has been increasing with the same pace that customer boards have become more sophisticated and require special properties. To survive as a high-end PCB QTA supplier in such a fast-changing environment requires world-class laminate partner network, fluent logistic arrangements, fast and efficient engineering team, and efficient stock handling procedures.
Final product dictates the needs
Within past ten years, amount of special laminates from different laminate vendors has been drastically increasing. This has been driven by end customer product PCB’s, which require more performance in more challenging environments. 5G has been driving higher electrical performance to manage higher frequencies and increased thermal loads in telecommunications segment; for automotive segment, hybrid and electrical cars require more robustness and more thermal conductivity to support higher voltage and -power as well as wider temperature ranges. Never-ending miniaturization race in consumer electronics requires thinner materials and higher electrical performance – just to name a few end-product qualities that translate into dielectric materials qualities. And all this should become with cheaper laminate price, of course.
Wider use and supplier base for example for lowest Dk/Df high speed materials are causing supply challenges from time to time – good news is, that availability has remained quite normal despite of the current pandemic. Highest performing materials are today typically using special class cloth types (Low Dk glass types, which glass DK is ~4.5 instead of ~6 for E-glass) and special, smooth copper foil types (Rz <2um) to minimize the signal losses on PCB. Production quantities for these special types are typically lower and there are not so many alternatives as for standard materials, so quick changes are slower to make. Nevertheless, demand for such special parts of the laminates are increasing, that will increase naturally also the production quantities in long run.
Good partners
Aspocomp has been making PCB’s over 40 years and during this time built a good relationship with all major global dielectric material suppliers. Most of the materials used today are coming from our five main partners: Elite Material Co. (https://www.emctw.com/en-global), Isola-Group (https://www.isola-group.com/ @IsolaGroup) , Panasonic Electronic materials (https://industrial.panasonic.com/ww/electronic-materials), Rogers Corporation (https://rogerscorp.com/advanced-connectivity-solutions @Rogers_Corp) and ShengYi Technology Co. (http://www.syst.com.cn/en/jtjs/index_146.aspx ) (in alphabetical order). Some of these suppliers have their production facility in Central-Europe, and rest have effective logistics to support Aspocomp QTA PCB production. Many of the materials from these suppliers are already qualified for production and normally there is some level of stock for small prototyping quantities. However, due to wide material- and thickness offering these companies provide, it is always good to confirm material availability in advance from your Aspocomp sales team contact.
And even if your PCB requires materials from other sources like our main partners, don’t hesitate to contact us – we have ways to support your needs and/or offer similar kind of alternative from our partners’ offerings.
By Mika Sillgren